


It gives a cut of width about 2.5-3.5 mm with a torch-to-work distance of about 10 mm when cutting with about 250A.OK just managed to get 20 minutes in the garage. The tungsten electrode may be of 1.6 or 2 mm diameter. The actual proportion of the gases will depend upon the nature of job or metals. Any combination of the gases can be selected at will to suit the material and thickness. Argon-hydrogen, and argon-nitrogen are also used for cutting. The gases used are argon, hydrogen, nitrogen also required is high voltage up to 300V an open circuit and about 170V during the cutting process. The arc is transferred from the nozzle and passes between the electrode and the ‘work’. It emerges as a high temperature ionised plasma stream. A gas mixture or air passes under pressure through the nozzle orifice and round the arc. The arc is struck between the electrode and conducting body of the torch or arc-holder. But plasma-cutting gives clean cuts at fast cutting speeds in aluminium, mild steel, stainless steels, and electrically conducting materials. All arc cuttings are based on the melting of the metal at the cut by the heat of an electrode arc.Īpplications of arc cutting include cast-iron, alloy-steels, non- ferrous metals as well as scrap metals.
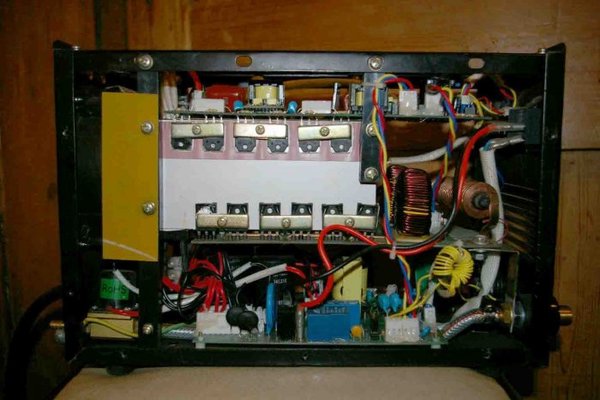
There are many processes for metal cutting-Flame (Oxy-cutting), Metal electrode, Carbon electrode, Air-arc, and plasma-cutting. The applications include valve seats, oil drill tool joints, gate valve inserts, diesel engine- cross-heads, etc. It is applicable on Cobalt-based, Nickel-based, Iron-based alloys with chrome or molybdenum alloys. 18.4 Plasma Transferred Arc container to the work in a stream of argon and is melted in the plasma, the argon providing a shield around the plasma heat zone. The powder feed rate is controlled by varying the feed opening over the knurled rotating wheel upon which a regulated ribbon of powder is supplied and the powder feed can be regulated to provide an up-slope and down-slope feed rate. The powder deposition process is fully automated and uses a solid state – SCR powder is supplied from a powder feeder operating on the rotating drum principle. More suitable applications are gas turbine parts, such as sealing rings of gas turbines, mixer and feed parts, sheets and wear pads, etc. The cobalt, nickel, and tungsten-based powders are supplied for this process.
